Understanding the properties of materials, such as their stress-strain behaviour, elasticity, and safety factors, is essential in designing robust and efficient structures. By applying these principles, engineers can ensure safety, optimize material use, and predict material behaviour under various conditions. Whether you’re stretching a rubber band or designing a skyscraper, these principles remain foundational. Materials play a pivotal role in structural engineering and other technical fields, as their behavior under various forces determines the safety and efficiency of designs. it delves into the core properties of materials, their response to forces, and their practical implications in engineering.
1.0 Properties of Materials
1.1 Introduction
When an external force acts on a material, it tends to deform. However, the cohesive forces between molecules resist this deformation. This resistance defines the strength of the material. Materials exhibit varying strengths, and their behavior can be categorized into two primary stages:
- Elastic Stage: Resistance is proportional to the deformation caused by the external force. Here, the material can return to its original state after the force is removed.
- Beyond Elastic Stage: Resistance diminishes as deformation progresses disproportionately until failure occurs. In this stage, the material experiences permanent deformation.
1.2 Stress and Strain
To understand material behavior, we define several key terms:
(i) Plasticity
Plasticity refers to a material’s ability to undergo permanent deformation in response to applied forces. For example, stretching chewing gum illustrates plastic deformation, as it does not return to its original form after being elongated.
(ii) Elasticity
Elasticity is the property that allows some materials to recover their original shape after the removal of deforming forces. For instance, a stretched rubber band quickly resumes its original dimensions upon release.
(iii) Stress (σ)
Stress is defined as the restoring force per unit area exerted within a material to counter an applied external force. The formula for stress is:
Stress (σ): Restoring force per unit area (Units: kN/m2, N/m2, kN/mm2, N/mm2)
- Formula: σ=F/A
(iv) Strain (ε)
Strain is the ratio of the change in length or volume to the original length or volume. As a ratio, strain is dimensionless. Its formula is:
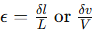
(v) Hooke’s Law
Hooke’s Law states that stress is proportional to strain within the elastic limit. Mathematically:
Or:
Where is the modulus of elasticity, a material constant that varies with the type of material.
Moduli of Elasticity
(vi) Young’s Modulus (E)
Young’s Modulus is the ratio of longitudinal stress to strain within the elastic limit. Consider a wire with an original length , a cross-sectional area , and an applied force causing an elongation . The formula for Young’s Modulus is:

(vii) Bulk Modulus (K)
Bulk Modulus is the ratio of stress to volumetric strain. If a force acts uniformly over a surface causing only volume change, the strain is volumetric.
(viii) Modulus of Rigidity (G)
This is the ratio of tangential force per unit area to angular deformation produced in a material. It characterizes a material’s ability to resist shape change under shear stress.
Other Key Terms
(ix) Working Stress and Ultimate Stress
- Working Stress: The maximum allowable stress a material can endure during service without failure. It is always less than the elastic limit.
- Ultimate Stress: The maximum stress a material can withstand before failure.
(x) Factor of Safety (FS)
The Factor of Safety ensures that materials operate well below their breaking point for reliability and safety. It is calculated as:

A safe system has , balancing safety with system efficiency.